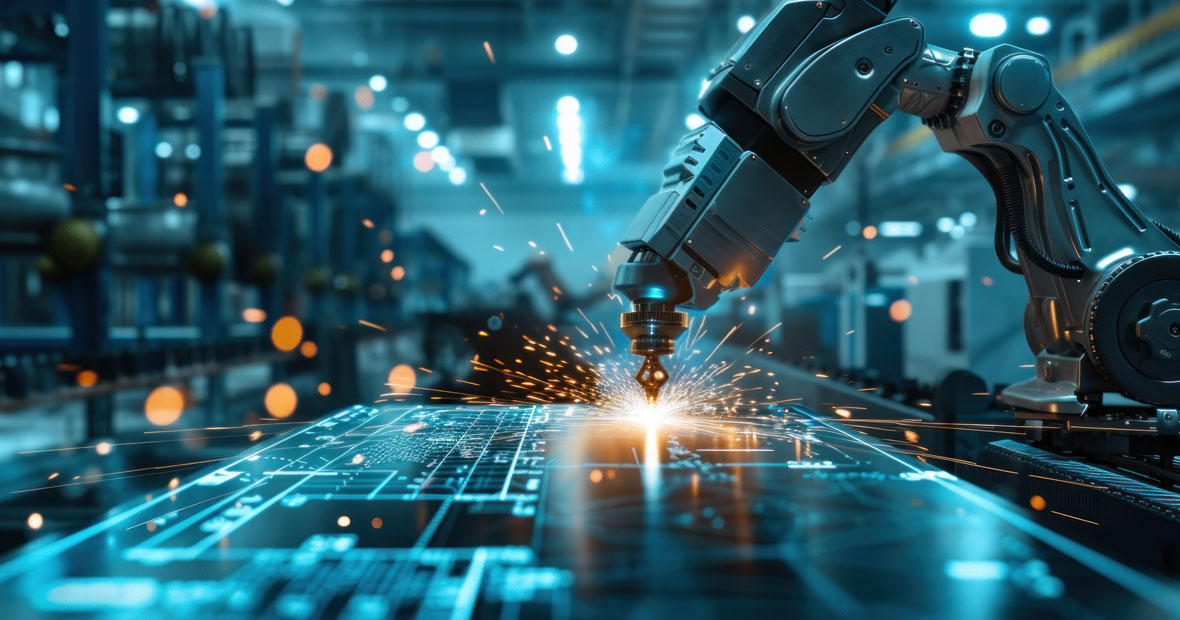
As advancements in technology permeate the industrial sector, friction stir welding robotics stand at the forefront, bringing about a significant shift in traditional manufacturing methods. These advanced machines, equipped with the prowess of automation, are transforming the welding world with their capabilities. This revolutionary technology provides high-quality joining solutions, customized to tackle the most intricate welding challenges. Further, friction stir welding robotics enhance production capacity while driving cost efficiencies, thereby reshaping the dynamics of the welding process. However, integrating these robots into the system does present challenges, yet with the right solutions, the potential benefits are immense. The future of friction stir welding rests on the shoulders of these advanced machines, holding immense prospects for the industry.
Revolutionizing manufacturing with friction stir welding robotics
In the realm of manufacturing, friction stir welding (FSW) technology is leaving a significant imprint, especially within the aerospace and automotive industries, where efficiency and durability are paramount. This method of welding is revolutionizing traditional manufacturing processes in sectors such as maritime, promising a future filled with potential emerging technologies that could transform energy and construction industries.
Innovations in robot-assisted friction stir welding for high-quality joining
Robot-assisted FSW is a game-changer, with advanced systems like KUKA robotics leading the way towards enhanced precision and flexibility. These machines, through their innovative technology, have revolutionized the process of friction stir welding, offering unprecedented control and quality in the joining process.
Customizing automation solutions for complex welding challenges
Automation plays a significant role in addressing complex welding challenges. Machines such as StirWeld offer customized automation solutions, which contribute to the reduction of production costs while improving the quality of assemblies. These systems have the potential to reshape the way small and medium-sized manufacturers approach their welding processes.
Improving production capacity and cost efficiency with fsw robotics
FSW robotics has emerged as a powerful tool for improving production capacity and cost efficiency. The integration of this technology into manufacturing processes has proven to be a cost-effective solution, enabling industries to increase their output while maintaining high-quality standards.
Enhancing quality and efficiency in welding processes through automation
Through the integration of robotics into welding processes, superior precision and quality control is achieved. This transformation is characterized by an impact of automation on the efficiency of both high and low-temperature welding processes. Advancements in control systems, inherent to robotic welding, maximize productivity, bolstering the value proposition of this innovative approach.
Robotic tools bring a plethora of benefits to the table, one of which is a significant reduction in welding defects. This consequently improves the quality of assemblies, underscoring the role of automation technologies in enhancing welding processes. Furthermore, automation plays a pivotal role in minimizing energy consumption, contributing to reducing the environmental impact of welding.
Automation also paves the way for the standardization of welding processes, ensuring consistent quality across all parts. The evolution of these systems and tools, coupled with the integration of robotics, revolutionizes the traditional welding process. The automation of these processes ushers in an era of unprecedented quality and efficiency, streamlining control and reducing energy usage.
In the context of Friction Stir Welding Robotics, automation with advanced machinery takes center stage. These machines, designed with high precision and control, lead to enhanced quality and efficiency in the welding process. With the advent of automation, a new era of welding has emerged, characterized by superior quality, efficiency, and environmental sustainability. By reducing defects and improving assembly quality, the role of robotic tools in the advancement of welding processes becomes undeniable.
Challenges and solutions in integrating robotics with friction stir welding
Integrating robotics into friction stir welding (FSW) presents both challenges and opportunities. On the one hand, the technical and practical obstacles are significant. The spindle speed, path, and the pressure applied by the pin on the materials to be welded require precise control, which is not always easily achieved with a robot. Moreover, training operators to handle these new robots poses another challenge.
On the other hand, the potential benefits of successful integration are vast. The quality and efficiency of production can be greatly improved with the use of a Friction stir welding machine. For instance, a robot can ensure that the head of the machine follows the appropriate path with a precision that would be difficult for a human to achieve. This can result in a superior quality of welding, especially when dealing with complex parts and components.
Recent technological advancements in this field have enabled better control over the process and have made it possible to overcome some of the initial challenges. New designs of machines and improved software have allowed for more precise control over the process, improving the quality of the welds and the overall production process.
The implications of these advancements for the manufacturing industry are profound. Not only does this mean improved quality and efficiency, but it also has positive implications for worker safety. Additionally, the use of robotics in FSW has potential environmental benefits, as the process can be more energy-efficient and produce less waste than traditional welding methods.
Looking forward, the prospects for further integrating robotics into FSW are promising. Innovative solutions are being developed to address the remaining challenges, and the economic impact of this integration is expected to be significant. Current and future trends point towards an increasing role for robotics in FSW, which will undoubtedly continue to transform the field.
Future prospects: the role of advanced robotics in friction stir welding applications
Understanding the benefits of employing advanced robotics in Friction Stir Welding (FSW) applications provides insights into their industry-altering potential. Advanced robotics amplify the efficiency and precision of FSW, a solid-state joining process primarily used in the welding of aluminum. The integration of advanced robotics in FSW has been successful, with numerous case studies bearing testament to its effectiveness. CNC Robotic FSW, for instance, offers an innovative solution to complex welding procedures, ensuring high-quality welds with enhanced structural integrity.
The future holds promising prospects for the role of robotics in FSW applications. Emerging trends indicate a surge in the use of robotics, with innovations being constantly developed to further the field. The use of robotic FSW in the production of battery cells, as exemplified by the Thompson friction welding machine, is one such innovation that is setting the pace for others to follow. Video tutorials or demonstrations, interviews with experts, and articles help shed light on how advanced robotics is revolutionizing the FSW industry.
However, the integration of robotics in FSW is not without its challenges. Solutions are continuously being sought to overcome these hurdles and boost productivity and efficiency. The positive impact of advanced robotics on the safety of FSW operations is another factor contributing to its growing adoption. Although an initial investment is required, the profitability analysis indicates a high return on investment in robotics for FSW, which is encouraging more industries to adopt this technology.