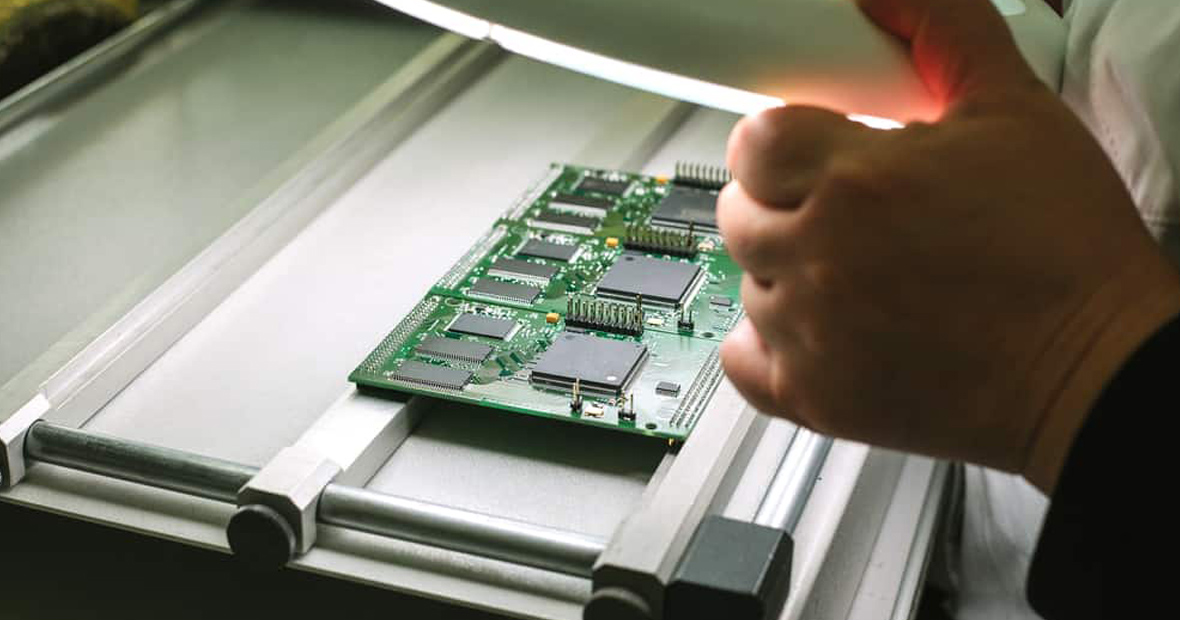
Venturing into the realm of Printed Circuit Board (PCB) design requires a keen understanding and application of Design for Manufacturability (DFM) principles. By seamlessly integrating these guidelines into PCB design rules, it's possible to streamline the transition from concept to production, ensuring efficiency and cost-effectiveness. This transition, however, is not without its challenges. From the outset, designers must be able to optimize their designs for manufacturability, synchronizing their design and manufacturing processes to reduce revisions and enhance circuit performance. The potential benefits of this integration are numerous, ranging from reduced production costs and time, to improved product quality and reliability. Despite the complexities of PCB materials and components, achieving DFM compliance is an attainable goal. This is made easier with the help of advanced software tools designed for DFM-driven PCB design and testing. These tools offer simulation and analysis capabilities to preempt manufacturing issues and leverage automation for increased DFM efficiency.
Embracing dfm principles for efficient pcb layout and design
An understanding of basic DFM principles is vital to optimize each layer of the printed circuit board. A strategic selection and arrangement of components, respecting DFM rules, can remarkably enhance signal integrity. By minimizing copper traces, costs are reduced without compromising PCB performance. The DFM guidelines serve to anticipate manufacturing issues and ensure design repeatability. A balance between aesthetics and functionality is achieved by integrating DFM requirements into the design process, resulting in a PCB that is both efficient and visually appealing. Designers can leverage DFM principles to improve thermal management through a strategic layout of layers and components. One key player in this field that has been implementing these principles is icape-group.com. The company has been setting the benchmark for efficient PCB layout and design, ensuring the optimal use of board layers and trace guidelines to maintain signal integrity.
Optimizing PCB Design for Manufacturability from the Start
The early integration of DFM rules into the design process is critical for efficiency. This proactive approach allows designers to foresee and address potential manufacturing issues, thereby reducing the necessity for costly revisions later in the process. It is imperative to strike a balance between the aesthetics of the circuit layout and its functional requirements, without compromising on either. The strategic arrangement of components and layers, guided by DFM principles, aids in maintaining this balance. Minimizing the use of copper traces not only brings down the production cost but also enhances the overall performance of the PCB.
Strategies for Synchronizing PCB Design and Manufacturing Processes
Synchronizing the PCB design with the manufacturing process by integrating DFM guidelines from the outset ensures a smooth transition from design to production. This alignment also aids in enhancing the performance of the circuit, maintaining signal integrity and managing the thermal properties of the PCB. The principles of DFM go a long way in ensuring the repeatability of design, thereby reducing the cost and time involved in the manufacturing process.
Impact of DFM on Reducing Revisions and Enhancing Circuit Performance
DFM plays a significant role in reducing the necessity for revisions and enhancing circuit performance. By anticipating and addressing manufacturing issues at the design stage itself, the need for adjustments during the manufacturing process is greatly reduced. This leads to cost savings and improved efficiency. Furthermore, the strategic arrangement of components and layers, guided by DFM principles, enhances signal integrity and thermal management of the PCB.
Reducing production costs and time through effective dfm integration
Design for Manufacturing (DFM) integration, when done right, plays a pivotal role in the reduction of production costs and time. A thorough cost-benefit analysis early in the DFM integration process is essential to minimize production expenses. Strategies for optimizing component placement can significantly reduce assembly time in manufacturing processes.
Computer-aided design (CAD) software has become the go-to tool for efficient and precise DFM integration. By using CAD software, designers can accurately predict the outcome of the manufacturing process, thereby reducing potential errors and associated costs. Simplifying manufacturing processes further by adopting DFM design rules that focus on reducing the number of parts is another effective strategy. This approach not only cuts down the cost but also saves time in the production cycle.
Material selection, too, has a profound effect on cost and time reduction in the production cycle. By choosing materials that are easier to work with and more readily available, manufacturers can drive down costs and speed up production. Collaboration across departments is key for a successful implementation of DFM guidelines right from the early stages of design. This collaborative approach ensures that all aspects of the manufacturing process are considered, leading to a more efficient and cost-effective production cycle.
Enhancing product quality and reliability with comprehensive dfm guidelines
In contemporary electronics manufacturing, the significance of Design for Manufacturability (DFM) directives cannot be overstated. These directives play a pivotal role in enhancing the quality and reliability of products. By adhering to DFM guidelines, it becomes feasible to foresee and mitigate potential production issues, thereby optimizing costs.
Early validation and testing strategies are integral for ensuring conformance to manufacturability standards. These strategies encompass rigorous quality checks and performance evaluations, which are instrumental in identifying potential flaws in the early stages of production. It helps in the rectification of defects promptly, preventing the escalation of minor issues into major complications.
DFM principles are applied to ensure that the design is aligned with manufacturing capabilities. Implementing these principles during the design phase aids in eliminating elements that could be challenging to produce, thus promoting seamless production.
The integration of DFM standards into the product development cycle is a methodical approach to improving performance. It involves a precise understanding of manufacturing processes and the proactive resolution of potential issues.
As technology evolves and market demands shift, the continuous evaluation and adjustment of DFM criteria become necessary. This approach enables manufacturers to stay ahead of trends and ensures that their products meet the ever-changing needs of consumers.
Navigating the complexities of pcb materials and components for dfm compliance
Understanding the significance of selecting suitable PCB materials in adherence with DFM guidelines is a vital aspect of electronic design. The right choice of materials can help optimize thermal compatibility and ease of soldering, which are crucial factors in the production process. Component density, too, has a direct impact on PCB fabrication and assembly.
Thermal management presents a significant challenge in PCB design for DFM compliance. The heat generated during the operation of the device must be effectively dissipated to avoid damage to the components and the board itself. Innovative PCB materials have been developed to help overcome these manufacturing complexities. These not only offer enhanced thermal properties but also provide improved mechanical and electrical performance.
Utilizing advanced software tools for dfm-driven pcb design and testing
The world of printed circuit board (PCB) design thrives on precision and efficiency. Advanced software tools play a critical role in enhancing these aspects, hence ensuring superior product quality and lower production costs. Modern innovations in PCB design software tools provide an array of functionalities that streamline the design process while adhering to Design for Manufacturability (DFM) guidelines. These tools aid in predicting potential manufacturing issues, thereby allowing for preemptive solutions and enhancing overall production efficiency.
Selection criteria for dfm-compatible pcb design software
Choosing the right software tool for PCB design necessitates a clear understanding of the project's specific requirements. It necessitates a careful evaluation of various software tools in the market, taking into account their features, ease-of-use, compatibility with DFM guidelines, and their potential to improve the design workflow. Expert advice often proves valuable in this selection process.
Integrating simulation and analysis tools to preempt manufacturing issues
Advanced software tools for PCB design offer integrated simulation and analysis features. These features facilitate the detection of potential manufacturing issues at the design stage itself, thereby minimizing production hiccups and reducing costs. It presents a detailed overview of the design process, thereby enabling designers to overcome potential challenges effectively.
Leveraging automation in pcb design for dfm efficiency
Automation is a key feature of advanced PCB design software tools. It aids in the efficient execution of repetitive tasks, reducing human error, and enhancing DFM efficiency. The integration of these software tools into the PCB design process is instrumental in streamlining the workflow, resulting in a robust and reliable product. With continuous advancements in technology, the future of PCB design software tools looks promising with more intelligent and intuitive features on the horizon.